After a lot of use, I've found molex microfits to hold up poorly to stress. I saw HEBI robotics using RJ45 and thought it might be a reasonable approach. I'm interested in brainstorming other possible connectors and seeing if there's something that will hold up to the use-case.
Connector Requirements
Cheap (hopefully < $3). That's the name of the game for this robot actuator.
High Power. I think we can easily pull 8-10A on accident and I'd rather not melt the connector in this case. It is worth noting that 21 Gauge wire hasn't had any issues with the normal arm load so I think I'm drawing a lot less power through the arm than I expected.
Microfit
Benefits
High current rating (8.5A)
Issues
The crimps used for microfit are folded sheet metal.
As the robot moves around, the cables have a small amount of motion. This ends up wiggling the crimped wires and slowly opens up this folded box. Once it's spread open enough, reliable continuity goes out the window.
RJ45
Benefits
To my understanding, RJ45 offers a highly reliable connection interface. I believe this is the case because of the spring system in the pin engagement. This allows the connector to wiggle without losing connectivity. I found some in-plane connectors on digikey (search query for reference) that will require some board re-design (as they will collide with the passives when stacked). But they have a shorter final height than the bulk caps which is a win!
The less optimal part is that there will be big board cut-outs.
The other big plus of RJ45 is that ethernet cables are dirt cheap. If we can just use cables off the shelf that would be awesome (however using any old cable will definitely not work).
Issues
The main concern I have overall with this method is current limits in the wiring and connectors. The connector referenced above has a 1.5A limit per pin. I was planning to use 2 pairs for power rails but that still only gives us 3A.
Cable flexibility is another big concern. In order to get enough power through the wires, I think 23 gauge wire is necessary. I saw a lot of potential sellers for this but it was always solid core wire instead of stranded. I ended up getting some just to fiddle with and found it waaaay too stiff to use in practice.
Very much a WIP/Brain dump. Feel free to comment.
After a lot of use, I've found molex microfits to hold up poorly to stress. I saw HEBI robotics using RJ45 and thought it might be a reasonable approach. I'm interested in brainstorming other possible connectors and seeing if there's something that will hold up to the use-case.
Connector Requirements
Microfit
Benefits
Issues
The crimps used for microfit are folded sheet metal.
As the robot moves around, the cables have a small amount of motion. This ends up wiggling the crimped wires and slowly opens up this folded box. Once it's spread open enough, reliable continuity goes out the window.
RJ45
Benefits
To my understanding, RJ45 offers a highly reliable connection interface. I believe this is the case because of the spring system in the pin engagement. This allows the connector to wiggle without losing connectivity. I found some in-plane connectors on digikey (search query for reference) that will require some board re-design (as they will collide with the passives when stacked). But they have a shorter final height than the bulk caps which is a win!
The less optimal part is that there will be big board cut-outs.
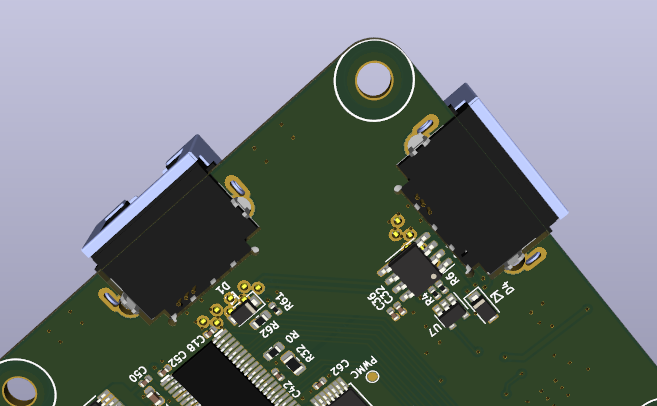
The other big plus of RJ45 is that ethernet cables are dirt cheap. If we can just use cables off the shelf that would be awesome (however using any old cable will definitely not work).
Issues