Open diglooo opened 4 years ago
Ouch... I can feel the pains of poor planner... And hunders, hundreds of hours spent making it work... How do you plan on integrating it with LA and S-Curve?
Shouldn't the RE motor motion just be X+E if the motors are mounted like the attached picture and E-X if the X and RE motor are coaxial and facing each other? Sorry but I have no clue about the inner workings of Marlin kinematics computations... :(
Without corrections - yes, in theory it's no different from CoreXY. In reality? At high speeds? I suspect extrusion will suffer after 70-80mm/s even without LA and Scurve. Though your idea doesn't make sense anyway. If you put it onto XY extruder Z bed - it'll just make one axis twice heavier, thus it's a massive downgrade. If you but it on XZ extruder Y bed - bed is still as heavy as motor, thus it's just useless.
For cartesian gantry style printers, like prusa, ender 3 and many others, the XZ carriage is already holding the weight of the extruder motor, the advantage of this solution is having a direct drive extruder without having the X carriage carrying the extruder motor around...
Il gio 14 mag 2020, 18:07 EvilGremlin notifications@github.com ha scritto:
Without corrections - yes, in theory it's no different from CoreXY. In reality? At high speeds? I suspect extrusion will suffer after 70-80mm/s even without LA and Scurve. Though your idea doesn't make sense anyway. If you put it onto XY extruder Z bed - it'll jsat make one axis twice heavier, thus it's a massive downgrade. If you but it on XZ extruder Y bed - bed is still as heavy as motor, thus it's just useless.
— You are receiving this because you authored the thread. Reply to this email directly, view it on GitHub https://github.com/MarlinFirmware/Marlin/issues/17995#issuecomment-628734062, or unsubscribe https://github.com/notifications/unsubscribe-auth/AO46MYWTTSZK4MBL7UXPSPTRRQJM7ANCNFSM4NAZH6NA .
Yep, but it doesn't make bed any lighter, so this is no better than pancake with gearbox or belt
Bed? The aim is to reduce the mass of a X carriage with a direct drive extruder assembly.
What's the point reducing mass of only one axis? Your speeds and quality only as good as heaviest carriage.
The point is to get at least one axis better. The bed stays at a constant height while printing; the X carriage is lifting upwards while printing and as a result you end up with a mass of ~200grams being accelerated back and forth at say 2000mm/s^2 at an height of 300mm from the bed surface if you're printing a tall model. The lighter the moving parts, the better... or not?
Yep, to an extent. Remember that while your light X carriage go up your bed become heavier and heavier... IMO, it's better to build proper rigid and heavy CoreXY and don't waste time on half measures.
Description
What if we have the filament drive gear remotely driven by a timing belt, driven from a motor located on the X carriage? This should achieve no-backlash, directly-driven and lightweight extruders.
This "remote extruder" (RE) motor will have to compensate the X motor movement in a differential fashion.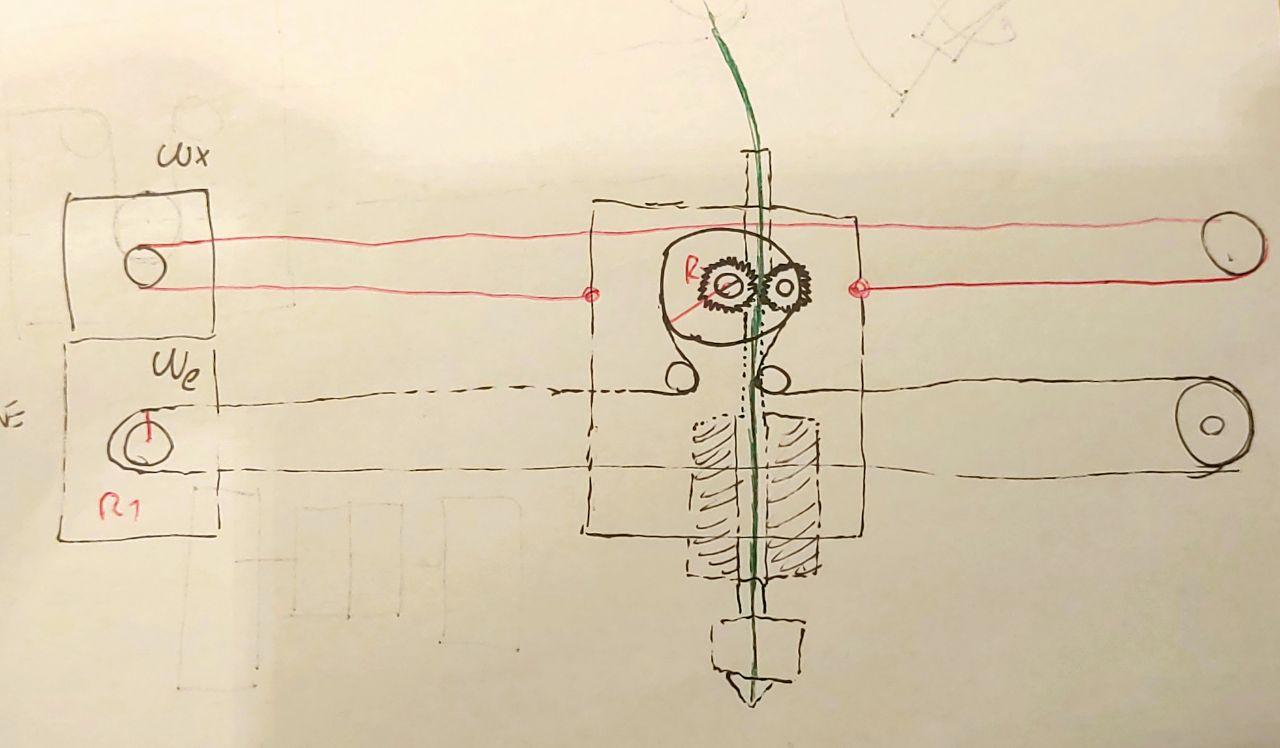
Feature Workflow
Users who adopt this feature will have to specify the details of the kinematic chain in the config file.
I have the skills and commitment to build the hardware, compile and test the software but I have no knowledge of the internal Marlin structure and working principle to autonomously implement this feature.
Cheers by diglo from Italy.