I would suggest 3 changes to the wheel roller area.
Tighten tolerances to the shaft of the roller, you can leave around 0.1mm or so
Add more space to the roller area. This reduces roller resistance and dirt affects driving less. I would suggest 0.3-0.5mm per side for spacing
To counteract the larger spacing per roller you can add a conical support to where the shaft connects to the roller. This reduces roller wobble.
Summary picture:
A small issue. The extruded part can not be too long since it can interfer with the rolling elements of the bearing. I would have the lip something like this:
How I achieved this:
defined a reference plane based on 2 edges to draw the sweep contour
redefine the sweep contour sketch plane to that reference plane
Check that the sweep works correctly (disable chain select)
I would suggest 3 changes to the wheel roller area.
Tighten tolerances to the shaft of the roller, you can leave around 0.1mm or so Add more space to the roller area. This reduces roller resistance and dirt affects driving less. I would suggest 0.3-0.5mm per side for spacing To counteract the larger spacing per roller you can add a conical support to where the shaft connects to the roller. This reduces roller wobble. Summary picture: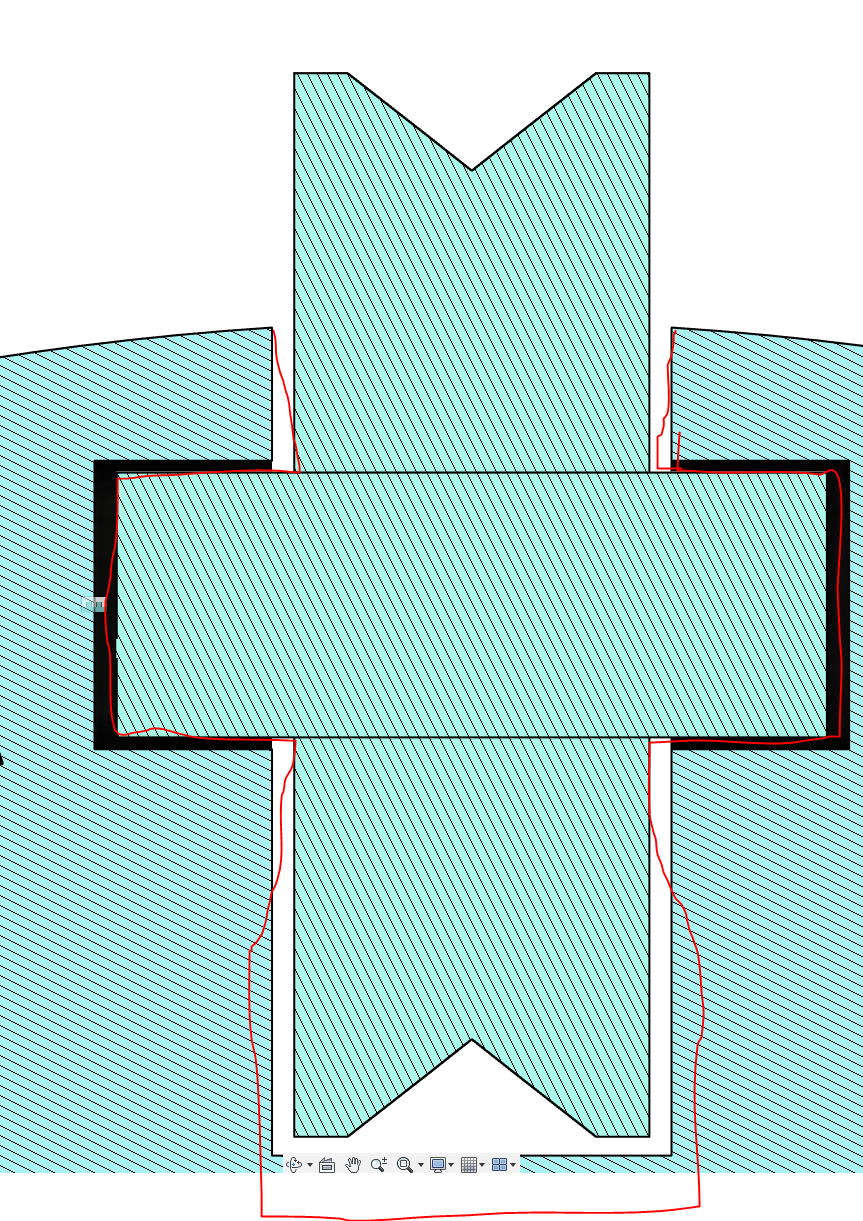